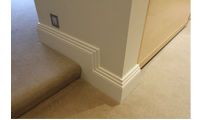
W.Howard’s Group Commercial Director Simon Fleet reveals how MDF can play its part in creating an environmentally friendly circular supply chain.
Awareness is growing of the need for efficiency at all levels of the construction supply chain – not just in how a building or system performs, but also in the way it is constructed.
It’s no longer enough for manufacturers to create single-use building products that are efficient while in use, but discarded once they are not required. Instead, the products and materials themselves should be recycled and reused wherever possible, to keep as much waste as possible out of landfill.
The more building materials can be recycled, the closer we get to creating a circular economy within the UK construction industry – something the government is keen to encourage in order to reduce waste production.
Earlier this year, the UK Green Building Council launched a two-year Circular Economy programme to develop guidance on how the built environment can be at the heart of a circular economy where waste is eliminated.
A circular economy is one that keeps materials in use beyond their initial product lifecycle, designing out waste and pollution right from the beginning. In practice, this means raw materials are used to create products and parts which, once no longer needed in the system they were created for, are collected for reuse, redistribution, recycling or remanufacture so that the raw material can be used again.
Recycling and reuse has always been a problem when it comes to MDF which, while being an incredibly popular building material thanks to its stability, consistency and smoothness, can be more difficult to recycle than some other timbers.
According to a report from the Waste and Resources Action Programme (WRAP), “around 1 million tonnes of MDF are used in the UK every year, with conservative estimates suggesting over 150,000 tonnes of MDF waste were either disposed of in landfill or burnt without energy recovery from the UK furniture sector alone”.
Keen to play its part in making the building industry more environmentally friendly, W.Howard has invested heavily in its production processes to ensure as much raw material is re-used as possible.
The MDF shavings, dust and much of the MDF waste generated by W.Howard’s MDF processes are sent to a local wood waste recycling company, and larger pieces of waste material that measure around one-metre in size are also gathered together onto pallets before being sent in bulk to local colleges and schools for use in their lessons, and to enable industry apprentices to practice their fitting and mitre joints.
We believe it is vital that the construction industry does everything it can to support the next generation of joiners and carpenters, both to help tackle the skills shortage and to ensure that knowledge of the traditional skilled wood trades is not lost over time. Supplying free materials wherever possible helps cash-strapped schools and colleges make the most of their finite resources.
Recycling MDF
Medium Density Fibreboard (MDF) is an engineered wood product composed of refined virgin wood fibres that are mixed with resin and wax before being pressed into flat sheets under pressure and high temperatures. Its smooth surface gives it a versatility that makes it ideal as a building material, as it is easily combined with a surface finish or paint to create an accurate and attractive finish.
The same process that makes MDF such a good building material does, however, use bonding chemicals that mean it cannot easily be recycled – until now.
W.Howard works closely with MDF Recovery, a business in North Wales that is dedicated to developing a technology for the recovery of wood fibres from waste MDF. MDF Recovery is currently working with one of the world’s largest producers of panel board products to scale up its technology for commercialisation.
MDF Recovery uses patented technology to strip the resins and laminates from the waste MDF wood, producing recycled wood fibres from 0.5mm to 3mm that are the same quality as virgin wood fibre, and which meet the technical specification for re-integration into newly produced MDF.
The BioComposites Centre at Bangor University is a Centre of Excellence in the development of wood-based panel technology, with more than 30 years’ experience of working collaboratively with the forest products sector. Using the expertise and pilot scale facilities of the Centre, MDF Recovery has successfully demonstrated the feasibility of recycling reclaimed MDF fibres back into MDF at pilot and multi-tonne industrial scales.
Centre Director Rob Elias explains: “This opportunity brings significant cost savings to the industry and demonstrates that MDF production can be a closed loop. Test results indicate no detrimental effect on board quality and, in some cases, we see actual improvements in mechanical performance and a reduction in panel emissions.”
The recovered wood fibres can also be used for other applications such as thermal insulation and horticultural growing media.
The process is chemical free and more cost-efficient, energy-saving and environmentally-friendly than landfill or burning – the usual options for the disposal of waste MDF.
With over 40 years-worth of MDF production in situ in the UK’s buildings and products, and more than 75 million tonnes of new MDF products being manufactured every year, it is vital that the industry finds ways to sustainably manage the full lifecycle of MDF production.
Explaining why he first became involved with MDF Recovery, Jonathan Grant, W.Howard’s Group Chief Executive, says: As well as my personal interest in protecting the environment, as a company we have always invested in ways of trying to ensure we are as environmentally friendly as possible. When we were approached to see if we were interested in investing in this process we jumped at the opportunity, as to be able to offer a closed loop supply chain is almost the Holy Grail in any manufacturing process. Once up and running we would hope to be able to offer our customers MDF moulding containing a percentage of recycled MDF as well as also being able to offer them a way to return to us any waste or used MDF they have as well.”
For more information on W.Howard’s comprehensive range of MDF products and profiles, visit whoward.eu.