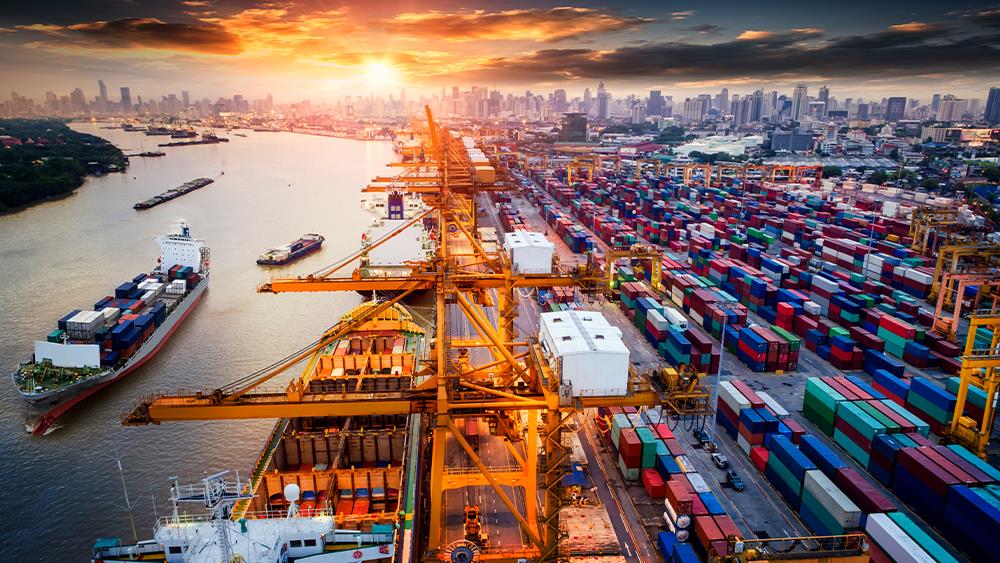
The first report of the year from the Construction Leadership Council’s Material Supply Chain Group (formerly Product Availability Group) shows 2024 starting in the same way that 2023 ended, with good levels of product availability and prices remaining flat or falling slightly.
As reported previously, the easing of pressure on product availability has largely been driven by continuing reduced demand across the different regions and sectors of the UK market, with those supplying housebuilders the worst hit.
New housebuilding continues to be held back by high interest rates and planning challenges. Larger builders do not anticipate a second half upturn at this stage. Regional mid-cap builders, however, cite the availability of small sites as their number one concern but expect to maintain current output levels throughout the year.
Any risks to product supply from the disruption in the Red Sea are yet to materialise, although the group is monitoring the availability and cost of supplies from the Indian subcontinent and Asia, such as decorative sandstone, plywood and sheet materials, hand tools, ironmongery, and electrical goods. A longer sea journey of 10-15 days has led to delays in deliveries, so the main concern here relates to five-fold price increases stemming from increased shipping and container costs for these products.
The group is also monitoring the supply of semi-conductors, which has been under pressure since the start of the pandemic. With four major design and manufacturing facilities in Israel, the conflict in Gaza has the potential to add further pressure on supply, and lead to increased prices.
Brick manufacturers have adjusted capacity to meet anticipated demand for 2024, while balancing stock levels. They recommend that all customers plan ahead, placing forward orders to maintain supply.
There is good availability of aggregates, cement and concrete, with demand not forecast to markedly improve until 2025, in spite of the current pipeline of infrastructure projects. There is also a plentiful supply of steel, but the supply chain here is under financial strain due to the downturn in demand.
Otherwise, there are concerning reports that late payment for materials is creeping up in a number of regions, although it is being managed at this stage. Obtaining trade credit insurance, however, is a bigger issue. Firms complain of coverage costing more and being reduced or withdrawn as insurers become more nervous about the level of construction insolvencies.
John Newcomb, CEO of the Builders Merchants Federation, and Peter Caplehorn, CEO of the Construction Products Association,the joint chairmen of the group are meeting with members of the Association of British Insurers to promote a greater understanding of building material supply within the wider construction landscape, with a view to changing insurers’ current blanket approach towards risk management.
Finally, the issues of labour costs, availability and skills shortages continues to rank high for most of the group' members. This ranges from concerns around a lack of resources among building control teams from 6 April to difficulties finding enough qualified site staff to support the transition to newer, more sustainable technologies and products. These concerns have been shared with the wider CLC and the group is continuing to have discussions with government and the Building Safety Regulator.