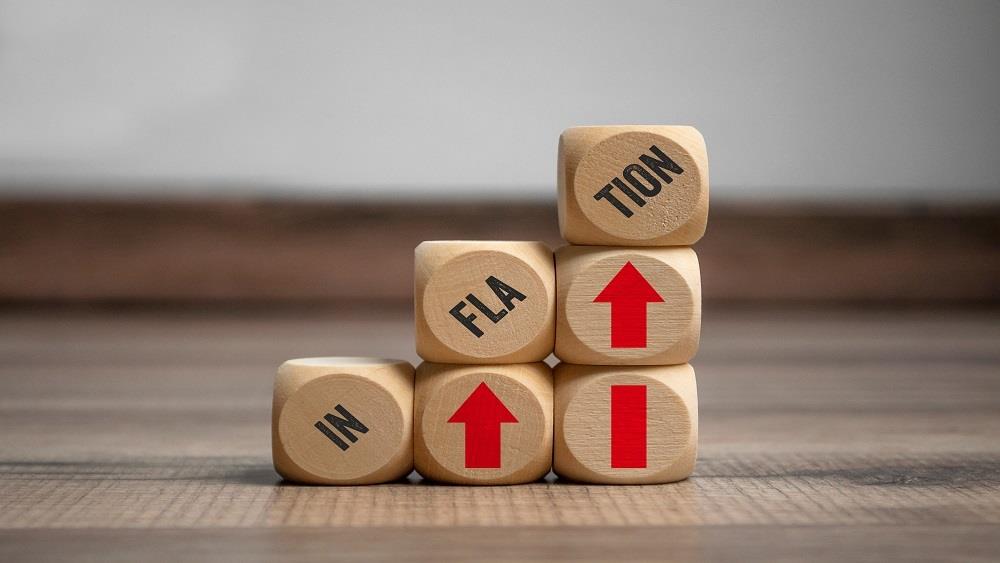
Jane Marsh, Editor-in-Chief of Environment.co, highlights the key areas where inflation impacts clients, contractors and their supply chain contacts.
Inflation occurs naturally over time. Even your grandparents’ loaf of bread is a fraction of today’s sticker prices. However, sudden jumps in inflation rates can push purchasing power downward and cost upward in extenuating circumstances, such as the pandemic.
Inflation affects more than daily essentials. Every industry faces a change, including the building industry. Construction inflation rose sharply at or above 20% from May 2021 to April 2022, resulting in the highest rates in 40 years. They have since decreased, but now is the time to evaluate how the building industry weathered the storm.
Unfortunately, inflation impacts clients, contractors and their supply chain contacts in these key areas:
Learning more about these stark industry changes makes it easier for impacted parties to prepare accordingly for inflation rate shifts.
Material costs and delivery times
The supply chain is one of the major areas of concern. As the power of the dollar drops, the costs of materials skyrocket. Contractors or construction companies operating on fixed rates and budgets have little room to adjust to price changes.
Materials are responsible for a considerable chunk of construction costs as well. They make up around 35-60% of overall costs, so an unprecedented change here could mean extensive loss.
Merchants and suppliers may face sluggish deliveries to these construction companies as well. Anything from windows to concrete may arrive weeks after they are needed, resulting in project delays. This could be a recipe for disaster, especially when combined with rising material prices.
Some companies are ordering materials weeks in advance or stockpiling to make headway on projects. Merchants and suppliers can help by fortifying their ability to fulfill large orders and make delivery more efficient.
Cost analysis, bid submissions and yearly budgets should also be flexible. If sudden drops or increases in inflation occur, flexible contractors can make the proper adjustments to stay within their profit margin.
On a more innovative note, green building is well-equipped to reduce material costs. Manufacturing and transportation of construction materials create a massive carbon footprint, but 3D printing can mitigate waste. Additive manufacturing directly on-site eliminates the need for costly and carbon-producing transportation methods. 3D printing concrete layers is also faster and more efficient.
Suppliers and shipping companies that want to aid this green effort and support timely construction processes should invest in greener technologies like 3D printing and recycled materials that reduce carbon emissions.
Auxiliary costs of energy and equipment
Materials make up the bulk of costs, but auxiliary components like fuel, machinery and technology prices accompany inflation increases. Crude petroleum fuels heavy equipment on a construction site, and rising prices could devastate renters and construction teams.
Construction companies must research their equipment needs thoroughly to mitigate energy and equipment costs. Renting heavy machinery is typically the norm, but buying equipment can be more cost-effective.
It’s more beneficial to make a one-time purchase if the equipment will be used more than 60-70% of the time. The company will now have a valuable asset in the long term and can take control of that machinery’s upkeep.
Scheduling frequent maintenance appointments can make equipment more fuel-efficient and run smoothly for longer.
Labour and compensation
Beyond physical goods, labour costs also rise with inflation. Experienced employees seek higher compensation in times of crisis. Additionally, an overall industry shortage of skilled workers leads to less experienced hires on projects. People who are not trained properly could lead to project delays and issues.
Construction companies must rethink their approach to labour-related costs and compensation. Offering more vacation and paid time off is often the most valuable asset. In fact, around 41% of workers valued this work/life balance more than a pay raise. It ultimately invigorates passion, attention to detail and company loyalty as people rest and recharge before the next project.
Cross-training allows companies to cultivate a skilled and versatile workforce that can address any project that comes its way. A strong and motivated in-house team enables companies to tackle more tasks quickly, with better results. The need to rehire or train from the ground up is nearly eliminated, saving on costs.
A proactive approach to inflation
Inflation can rock the foundations of any industry, but material costs and timelines are of the utmost importance in the building sector.
Certain challenges come with rising inflation rates for construction teams nationwide, but professionals can make proactive choices to prepare for heightened and unexpected expenses.