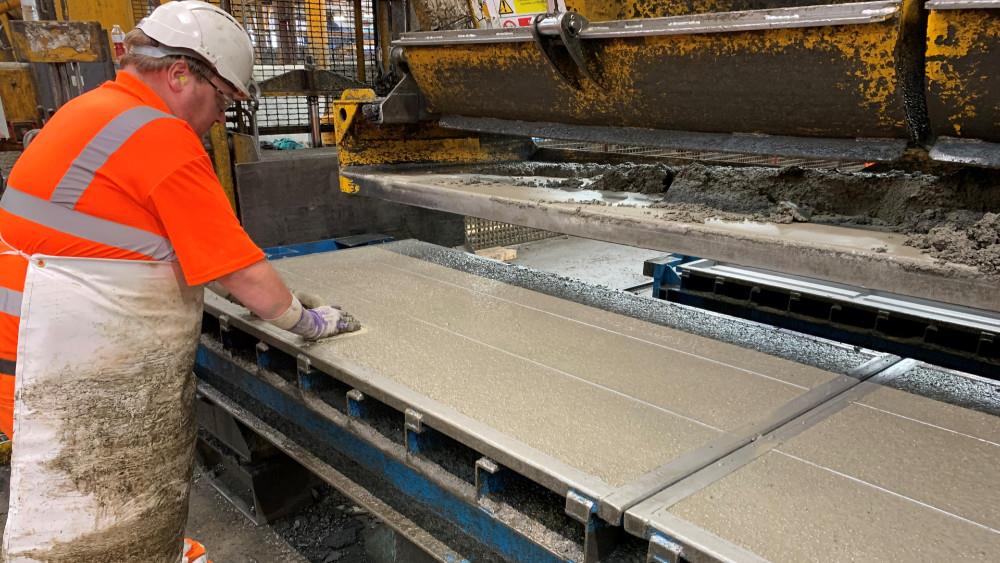
Ibstock Concrete is implementing substantial investment across its extensive UK manufacturing facilities to improve the safety and efficiency of its operations by undertaking innovative upgrades to its engineering practices.
Following extensive employee feedback, Ibstock Concrete has made significant upgrades to the manufacturing processes at its Bedford and Northwich sites, which make a comprehensive portfolio of landscaping, flooring, building, rail and infrastructure products.
At its Northwich facility, Ibstock Concrete has achieved an industry leading approach to the casting process, which consistently reduces the trigger time for vibration to below the HSE’s Control for Vibration at Work Regulations 2005 Daily Exposure Limit Value.
Following an in depth review of the existing casting process, which involved filling moulds with concrete and applying vibration at 55Hz to remove any air voids, a three stage visual indicator and three level vibration system has been installed.
This process is not only a new concept for Ibstock Concrete, but is a revolutionary approach for the entire industry, as it effectively reduces the associated risks of high levels of potential exposure to vibration, by providing individuals with real time information on the level of vibration the manufacturing equipment is currently operating at.
Even on the highest setting, a vibration survey has evidenced the potential exposure limit as low as 2.7 m/s2 A(8), while on the lowest setting, the potential exposure is as low as low as 0.5m/s2 A(8), both of which are below the HSE’s Daily Action Limits.
Ibstock Concrete has also reviewed its slotted post casting process at its Bedford facility. Following extensive employee consultation, reducing the frequency of manual handling required was identified as a key priority, to ensure the consistent safety of all operatives, without affecting the overall manufacturing process.
As a result, a central element of the production process has been automated through the installation of a dedicated rebate lifter, which mechanically lift the rebate from the cast product.
This eliminates the operator having to physically lift the rebates from the mould, substantially reducing the level of manual handling required by the operator.
The automation of this process is a completely new approach, again not only for Ibstock Concrete, but for the entire industry, as it modernises a traditional and established stage of the casting phase.
This technology is now being implemented across all relevant Ibstock Concrete manufacturing sites throughout the UK, providing an even safer working environment for employees by considerably reducing manual handling with the aid of mechanical means and in accordance with the HSE’s Manual Handling Operations Regulations.
Darren Waters, Managing Director of Ibstock Concrete, said: “As a company at the heart of building, Ibstock Concrete is committed to consistently ensuring the highest standards of safety by continuously improving our Health and Safety culture, which is built upon a zero harm philosophy.
“By taking a unique approach to our manufacturing processes and working in collaboration with our employees, we have been able to effectively upgrade our operations to ensure potential risk is reduced, without impacting operational proficiencies or product quality.
“In doing this, we have achieved completely new methods of manufacturing that raise the bar for reducing operatives’ exposure to vibration and the level of manual handling. We are extremely proud of our commitment to achieving the highest standards of health and safety and we are working in partnership with the British Precast Concrete Federation to aid the wider industry in successfully implementing safer manufacturing processes.”