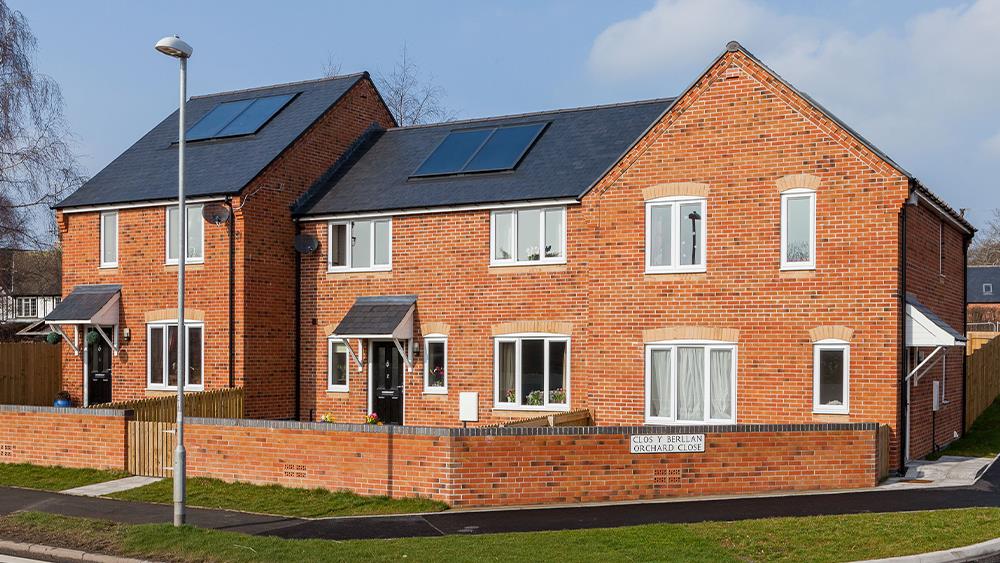
Steve Wharton, Manager at MPA Masonry, explores the opportunities to be had for savvy manufacturers, merchants, specifies and developers alike.
The string of seismic global events which have occurred over the past two years, of which the Russia-Ukraine war is just the latest, has exposed the fragility of supply chains we once thought secure.
Indeed, the building products sector was hit by one challenge after another from the Ever Given container ship trapped in the Suez Canal to the various energy and fuel crises of Autumn 2021. That’s before touching on the impact of Brexit and the aftershock of COVID-19.
Of course, these issues have had a knock-on effect, impacting myriads of other sectors, particularly for builders’ merchants facing shortages of many essential materials and components. In turn, this scarcity caused severe delays in the wider construction industry, pushing back start and completion dates resulting in excess costs for developers and contractors, with no return.
A quick look at market intelligence firm Glenigan’s various reports over the last six months shows the extent of this decline, with housebuilding hit particularly hard. Its most recent Index showed output in the vertical had declined 46% in February 2022 compared to 2021. Of course, it’s an unsustainable situation and something’s got to give soon, especially if we want to get back on track.
For me, this requires an immediate and far-reaching audit of the materials we import, and where we can realistically use domestically produced alternatives. Representing a category where around 95% of product in the UK market is locally sourced and produced, I’ve been able to observe the advantage of these small supply chains first-hand.
Equally, there are many other materials available on the home front, whether in raw form or manufactured from recycled materials of which we could be taking more advantage. Of course, there are some limitations; for example, it’s difficult to build a pitched roof without timber.
However, the lack of certain materials could become the catalyst for a new age of innovation, in design and material terms, looking at the very vernacular to accommodate future material shortages.
It will also evolve construction methods as contractors are encouraged to build leaner, but higher quality, assets. In turn, these benefits can be passed onto the occupant.
For builders’ merchants, it could prompt a reappraisal of product ranges and look to more locally sourced materials to mitigate supply chain and potential stock level issues.
Finally, the reduced amount of shipping will benefit all. Locally sourced material means less transport from factory, depot or merchant, resulting in less fuel used in shipping materials to site.
While this is no ideal situation, there are some silver linings, and there are opportunities to be had for savvy manufacturers, merchants, specifies and developers alike.
We need to seize them now. The geopolitical situation will likely intensify and a focus on reaching Net Zero will certainly put pressure on those shipping heavy materials over long distances. Closer to home, there’s a housing crisis growing more acute by the year which we urgently need to resolve.
This much is clear: the age of cheaply imported material is drawing to a close and we must make plans to meet the challenges of both today and tomorrow. Perhaps adopting a more local approach to the building product supply chain can provide part of the answer?