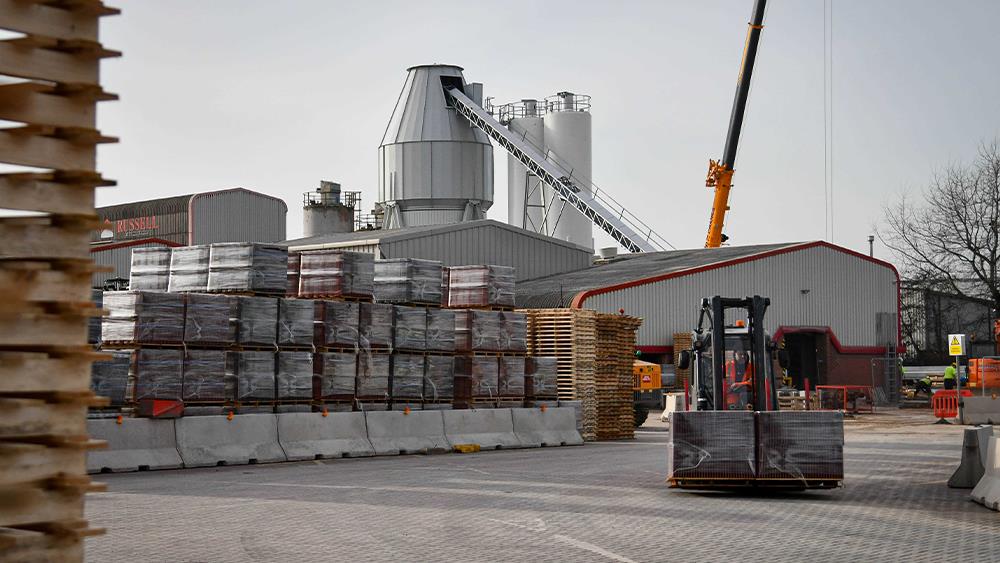
The project is the largest single investment since the manufacturer was acquired from Cemex in 2011.
As part of its major investment project at its Burton on Trent tile plant Russell Roof Tiles is installing state-of-the-art equipment which will support the firm’s Net Zero ambitions.
Russell Roof Tiles, is the leading independent manufacturer of concrete roof tiles and last year it announced a milestone £18.5 million investment programme, which should be complete by later in 2024.
Part of the project includes the installation of new state-of-the-art Skako Concrete ‘High Silo’ batching plant, complete with AM2250 planetary mixer to facilitate increased concrete roof tile production. Installation should be complete by Easter.
This whole project is the largest single investment since Russell Roof Tiles was acquired in 2011 by Crown Global Equity, which manufactures concrete roof tiles in the US and Mexico. Since then, the UK company has seen £17.3 million invested in its three sites, continuing to increase efficiencies and capacity to meet demand.
Not only is the new batching plant being installed while the tile plant continues to manufacture, it will have increased efficiencies as well as sustainable benefits such as a water reclamation and refiltering system, that allows for recycling of all wash water, including using wash water from the factory.
Russell Roof Tiles has been actively seeking ways to reduce its environmental impact, including investing in more energy efficient equipment, optimising its production processes, and sourcing more sustainable materials as part of its net zero pledge.
The company wants to become carbon neutral by 2040, ten years ahead of the government’s timeline.
The new Skako Concrete batching plant replaces Russell Roof Tiles' old and inefficient 1990’s batching plant and concrete mixer and was designed to meet increased production demand as well as allow for further capacity increases in the future.
The much larger volume system will be able to handle the sand, cement, and pigment needed to feed a new mixing plant and in-turn roof tile production line.
Bruce Laidlaw, Operations Director at Russell Roof Tiles, said: “It is important that we continue to focus on efficiencies and sustainability across this major project, looking at market leading environmental options throughout the new facility. For example, this type of mixer is up to 20% more energy efficient than alternatives available.
“Other energy efficiencies include using gravity to feed sand into the mixer below. Over time this saves a huge amount of energy moving sand. The Skako Concrete solution of holding such amount of sand above the mixer has allowed for the footprint to be compressed and thus install the full equipment within a much smaller area.”
Further benefits of the new equipment will include two 100T cement silo’s allowing for more flexibility in receiving cement deliveries, allowing Russell Roof Tiles to take volume cement deliveries around the clock and avoiding peak traffic times.
Utilising the latest technology, the system also provides remote operating from the factory floor, as well as remote diagnostics to minimise down time.