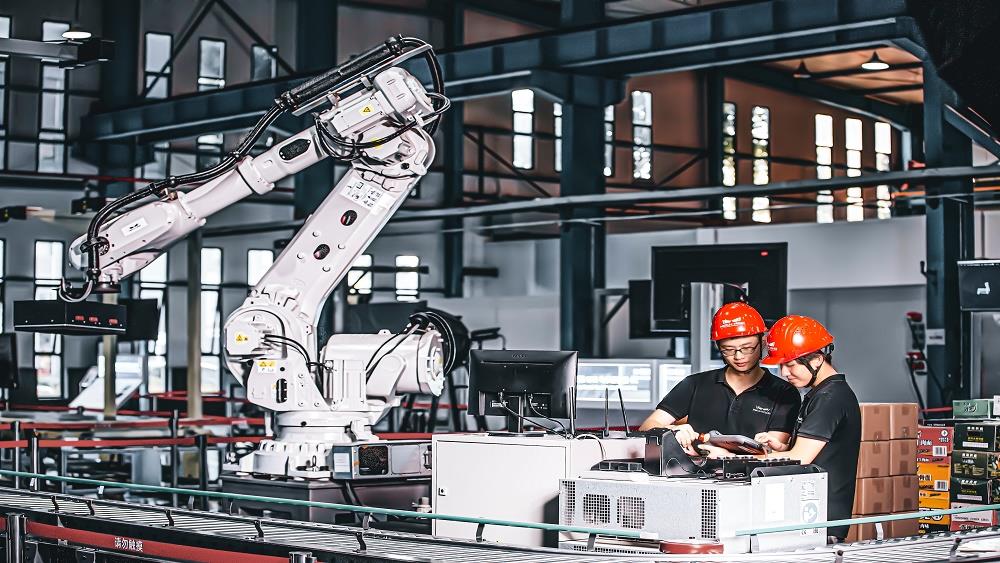
Trina Wilkinson, PHR, Talent and PeopleOps Manager at Evotix, a leader in EHS software solutions, offers advice on how an aging workforce in manufacturing can bring value to businesses and employees alike - and by preparing for it, leaders are setting themselves and their teams up for success.
A diverse workforce can be tremendously beneficial for manufacturing businesses. Having employees from different backgrounds, generations and cultures creates significant diversity to positively power your business, driving new ideas and collaboration opportunities not previously available.
Additionally, the ability for new professionals to learn from older, more mature professionals is a positive bi-product that a business often counts on, but can’t expect. And part of that expectation falls on the aging, older generation. Particularly in manufacturing, the industry is facing a shrinking talent pool as employees age out of work.
An aging workforce can bring distinct advantages for both the business and employees within the manufacturing industry, according to Evotix:
While businesses and leaders should recognise these values and harness the relevant employees to set themselves and their teams up for success, it’s hard to overlook the talent deficit that’s likely to come not just from an aging talent pool, but a talent shortage as well.
Finding and training younger talent to replace experienced employees is becoming increasingly difficult.
So what can manufacturing businesses do to address the loss of older workers?
Know your employees
While simple and straightforward, it is crucial that HR and management teams understand the demographics within an organization. Use data and analytics to gauge insight from the workforce. From this, there will be trends and data to interpret, such as absenteeism, a heavy shift of older workers, healthcare issues, etc.
Understand the needs of older workers
Every employee will have differing needs from their employer, but there may be some patterns and similarities among generations. Health and wellbeing policies should be catered to the workforce and kept up-to-date. Older employees tend to need more healthcare support than their younger counterparts.
HR teams need to adjust their health and wellbeing policies to accommodate these potential health risks to keep these employees in the workforce.
Knowledge transfer from older to young workers
Mentorship and apprenticeship programs are a great way to pass skills and information between generations. Manufacturing businesses should give the aging workforce the opportunity to connect to a new generation of employees. This connection should be bi-directional and allow the younger generation the opportunity to teach the older generation new skills and vice versa.
Harness technology
The right technology can create advantages and opportunities for older employees. Additionally, technology has the power to boost productivity, increase engagement and reduce turnover for today’s evolving teams.
Modern software solutions, such as manufacturing health and safety software, are becoming more sophisticated and versatile not only in terms of functionality but usability and simplicity as well. This can greatly help an aging workforce struggling to keep up with changes in workplace technology.
Maximizing the longevity of older workers’ careers
Some best practices to help companies retain their older workers and maximize their productivity until new talent can be acquired include using automation to handle repetitive manual labor, so older workers can prioritize tasks that require their unique skills and knowledge.
Depending on physical ability, businesses should allow workers to transfer internally to another position, as well as offer flexible hours or phased retirement.
Prepare new leaders
With the shortfall in talent and the transition of retiring workers, manufacturers need to create a succession plan for those who leave. Identifying early on in the careers of young talent if they prefer to be individual contributors or managers will help identify who to support as they move up within the organization. Individual contributors should be paired with experts in their trade to ensure as the aging talent pool exits, there’s a person ready to take on the new role.